Welding
CI welding technicians are fully certified to ASME Section IX Standards. PCI has access to a large database of qualified pipe welders for application of welding high pressure, high value, piping that is 100% volumetrically inspected. Our disciplined training and recertification programs promote customer confidence in our ability to deliver first time quality. We offer a full complement of manual and machine welding processes including Shielded Metal Arc Welding (SMAW), Gas Tungsten Arc Welding (TIG) (GTAW), Flux Cored Arc Welding (FCAW), Gas Metal Arc Welding (MIG) (GMAW), and Autogenous Fusion Welding for just about any alloy, including more exotic materials such as 410 SS, Inconel, P-91, and Super duplex.
We have the ability to weld any pipe or tube greater than ¼ inch to unlimited diameter and wall thickness. This is accomplished by having an extensive inventory of manual welding equipment and specialized orbital and track mounted welding heads for a variety of repair or replacement applications including pipe, fittings, valves, pumps, heat exchangers and other equipment. We can weld all types and grades of carbon and stainless steel materials.
Orbital Machine GTAW Welding
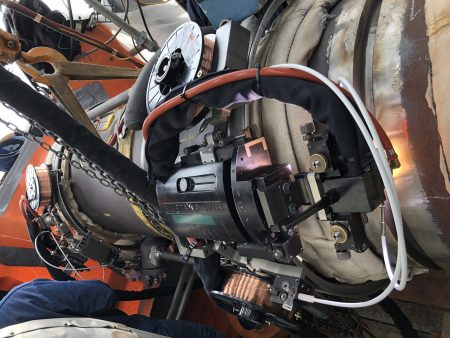
Machine Welding of Heavy Wall Main Steam Piping
In addition to our manual welding capabilities, a full inventory of orbital welding equipment enables us to handle any machine welding job. PCI offers a platform design for a GTAW, orbital welding system designed to be robust and simple-to-operate. Machine welding can be applied direct view or via our patented weld viewing system remotely operated, depending on the application. The GTAW system offers:
- A modular base for easy field troubleshooting, thus minimizing system downtime
- Standard power supply and water cooler
- Real-Time Data collection, storage and acquisition (USB port on controller)
- Selectable operator parameter limits for optimal weld quality
- Pendant design with logical menu navigation for intuitive, simple operation on a kilojoules pendant display (a key element in welding specialty alloys)
Narrow Groove Welding (NGW)
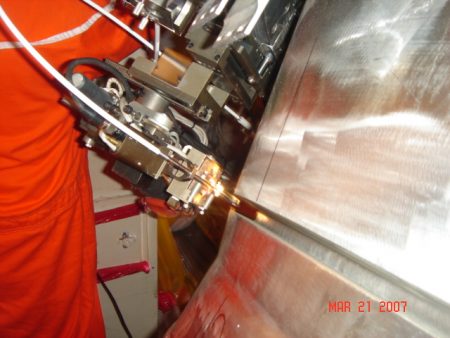
Narrow Groove Weld Reactor Coolant Piping
NGW has developed significantly during the past decade, and its benefits are widely recognized throughout the industrial sector being; increased production, reduced weld volume, reduced residual stresses, and reduced heat affected zones are among the advantages. The narrow groove joint design incorporates a two to five degree weld preparation, significantly less than the conventional weld bevel angles. NGW equated to up to 70% less weld material applied as compared to more conventional weld joint geometries. PCI’s narrow groove welding equipment was designed for both high weld quality and optimal usability and is typically preformed using our weld viewing system depending on the application. However, there are definitely applications where direct view machine welding is more cost-effective. One of our strengths is working with customers to apply cost-effective solutions to meet their welding requirements.
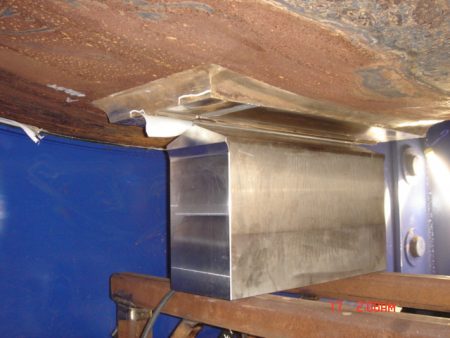
Steam Generator Key Lug Support
Mechanized Track Mounted Orbital GMAW / FCAW (High Deposition) Welding
Mechanized welding is a reliable way to weld out conventional weld joints using a high deposition welding process. PCI has the ability to us e this process on carbon, chrome alloy, stainless steel and other high nickel content based alloys. The process can make high quality welds up to 4 times faster than typical GTAW machine welding processes. Welds made by this technique deliver first time quality with faster weld-out times to help meet the demands of today’s aggressively scheduled maintenance outages.
- Track Mounted Semiautomatic MIG Welding
- Key Lug After GMAW Track Mounted Welding
Special Welding Applications
PCI also develops welding equipment and processes to address unique issues like low profile machine welding application, underwater GTWA welding, bore welding, robotic welding and spent fuel canister welding etc. For a specific specialty welding applications contact us.
![]() Remote Weld Overlay Weld Heads |
![]() Underwater GTAW Welding System |
Valve Repair and Replacement
PCI utilizes a variety of specialized portable boring bars, flange facers, end prep tools, drilling, MDM and EDM, milling, grinding and welding equipment to accomplish a full line of in-line repairs on valve bodies, studs, seats, guides, and flanges for valve repair in any industrial environments.
While removable valve parts such as gates, poppets, bonnets, and operators can be repaired in the field, it is frequently more cost effective and quicker to have these parts repaired in a traditional machine shop or valve repair facility with stationary equipment. Our machine shop in Rock Hill, SC can perform most repairs on removable valve parts.
![]() Loop Stop Isolation Valve Guide Installation |
![]() Loop Stop Isolation Valve Remote Welding |