Metrology
Critical to the successful execution of any type of project is the ability to measure accurately. At PCI, we are very sensitive to this and offer a wide array of Metrology Services. Our metrology engineers and technicians are well trained to provide customers with the best knowledge and experience in the industry associated with precise and accurate installation of components and mechanized systems. At PCI, we have no tolerance for inaccuracy which sets the stage for a successful implementation in the field.
PCI uses the latest technologies as defined below for all high accuracy surveying. Our metrology engineer will work with our customer to determine the most cost effective technology suited for their surveying application.
Laser Tracker and the “Templating” Process

Laser Tracker
Typically, PCI uses a Laser Tracking Interferometer System to perform measurements and surveys for large component replacement.
The process is broken down into three phases being:
- Survey of existing plant condition and old component support structure,
- Survey of the new replacement component and support structure, 3D modeling, and machining of the new component interface locations and
- Survey of the old piping and support structure after removal of the old component and machining of the existing piping.
During machining of new replacement component and existing plant piping and interface location the Laser Tracker with the real time coordinates is used to Laser align the machining equipment to assure first time fit-up of the replacement component. This proven technology has been used to successfully fit-up over 200 steam generator at nuclear plants, gathers target position information in a 3D spherical coordinate system.
The system is based on a single-data-collecting instrument that greatly simplifies the setup and relocation of the system hardware in a congested work environment. The laser tracking system can collect a large number of data points in a short period of time, with the advantage that the data is collected Real Time with no post processing required to ascertain validity.
- Accuracy to 0.0005 inches is achievable
- Measuring is viewed in Real Time display mode constantly
- Trackers mechanically align and track the target, reducing sighting errors and increasing accuracy
- Automatic leveling system for aligning data level to earth
- Measuring of large working volumes up to 110 foot radius from one position, and industrial and construction site proven
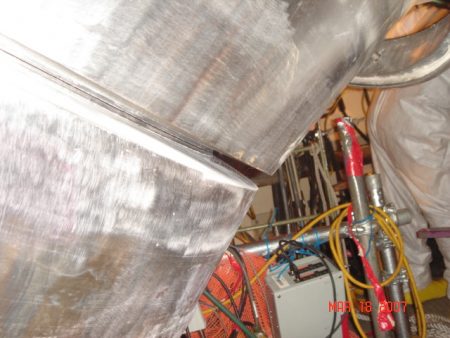
Fit-up of a Narrow Groove Weld Machining Tool Aligned by Laser
3D Laser Scanning
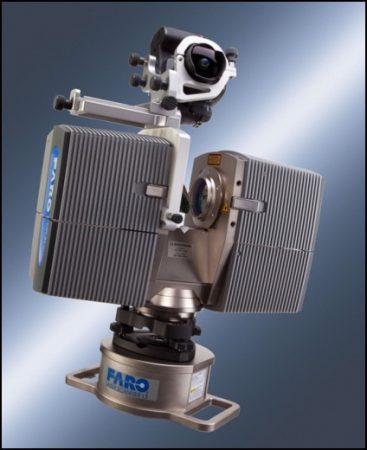
Laser Scanner
Laser scanning is a non-contact measuring method which uses a laser beam to find the 3D position of a point on an object’s surface. By repeating this process several million times the laser scanner is producing a so called “point cloud.” This point cloud is a precise capture of a physical object’s size and shape and can be imported to a computer for further treatment and visualization.
Laser scanning is used in many industrial applications where fast accurate survey of large structures, and/or components is required; typical applications include plant as-built surveys, new component surveys, plant modification planning to verify if new components will fit into existing plant configurations, walk-downs, rigging path verification, and applications where large amounts of components or area need to be accurately surveyed or mapped.
PCI has several types of laser scanning equipment including pedestal mount and hand held with varying degrees of accuracy. Please contact PCI for more information on laser scanning and which scanning technology would best fit your application.
- Accuracy to 0.125 inches is typical with these systems
- Large quantities of scanned measurement data is captured quickly (up to 360,000 points per second)
- Scanning data is used to create Virtual Models and Clash / Crash detection for rigging path analysis
- Archived scanned data can be performed off site at a later date or as needed for future data extraction
3D Model from Laser Scanning Actual Picture of Scanned Area
Digital Photogrammetry
PCI recommends and utilizes digital photogrammetry in areas that don’t lend itself to traditional measuring equipment. Areas where measurements need to be acquired from an unstable base such as a boat or projects that require the measurement of an object in motion can now be frozen in the split second it takes to snap a picture. Multiple pictures are taken of an object or area from different perspectives. Using known scale and reference points, we’re able to link together and create a 3D block or mosaic of the pictures. Once the blocking and bundling process is complete, measurements, locations, and objects can be extracted from the imagery. Accuracy, directly comparable to that of the theodolite and tracker surveys, is achievable with the photographs. One of the great advantages to the photogrammetry survey is the abundance of information captured during the survey. Once information is frozen in a photograph, it is captured and available to be modeled as needed.
- Accuracy to 0.001 inches is achievable.
Total Station Theodolite
PCI utilizes the latest technology in total station advancements. The system incorporates an infrared distance meter with a motorized tracking movement. Precise measurements can be acquired without the optical human sighting error previously incorporated with other instruments of this type. Utilizing angular measurement in the horizontal and vertical axis, along with its distance meter, the total station theodolite will provide 3D coordinate measurements for targeted control points and features.
- Accuracy of 0.01 inches is typical with target mode capabilities to 0.005 inches
- Measurements can be viewed directly after recording the measurement
- Light, robust, and portable with quick setup and relocation time
- Automatic leveling system for aligning data level to earth
- Measuring of large working volumes up to 400 foot radius from one position
- Industrial and construction site proven
3D Modeling and 3D Animation
PCI can take raw survey data from any of the technologies listed above and generate graphically accurate 3D models. Three-dimensional (3D) models represent a physical body using a collection of points in 3D space, connected by various geometric entities such as triangles, lines, curved surfaces, etc. Being a collection of data (points and other information), 3D models can be created by hand, algorithmically (procedural modeling), or scanned. Their surfaces may be further defined with texture mapping.
Animation is all about generating a chain of drawings or pictures taken by way of a simulation procedure for creating movement. It is a type of optical illusion through which we are able to see still images or drawings moving. The procedure involves the manifestation of motion as a result of displaying still pictures or photographs one after the other at the rate of 24 pictures per second. A video program or motion picture is considered one of the most common methods of presenting animation.
3D animation is helpful in graphically presenting to an audience that may lack technical understanding of the project; which could include plant modifications, heavy rigging, on-site movement of large components, construction progress, material process line sequence, etc..
3D modeling and animation can be time consuming and expensive, and is not required for all surveying applications. Please speak to a PCI representative to discuss your surveying and 3D modeling and animation requirements.